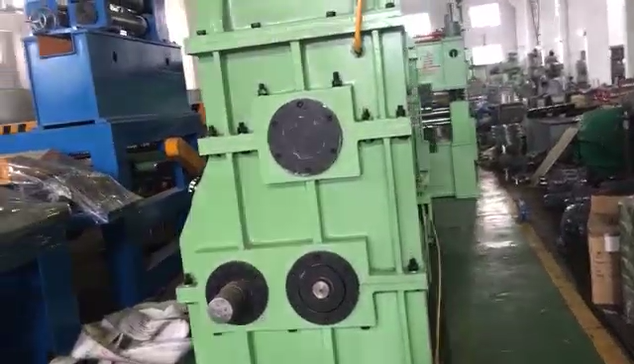
Innovative Application of Rotary Shear Technology in Metal Processing Industry
In the rapidly evolving metal processing industry, the demand for precision and efficiency has never been higher. Rotary shear technology, once a niche approach, has now emerged as a game-changer, revolutionizing the way metal sheets and plates are leveled and cut.
Rotary Shear Technology: The New Frontier
Rotary shear technology utilizes a rotating blade or cutter to precisely level and cut metal sheets. Unlike traditional shearing methods, rotary shear offers a continuous and non-stop cutting process, eliminating the need for intermittent stops that can lead to micro-indentations and other surface defects. This technology is especially suited for high-precision applications requiring minimal material distortion and maximum surface quality.
Serial Line: The Workhorse of Rotary Shear Technology
The serial line is the backbone of rotary shear technology, designed to handle a wide range of materials including CR, S.S., Al, and more. This versatile system is capable of precision leveling and cutting, ensuring that every product meets the strictest quality standards.
Continuous Cutting: The Key to Efficiency
One of the most significant advantages of the serial line is its ability to perform continuous cutting without interruption. This eliminates the downtime associated with traditional shearing methods, significantly increasing production efficiency. Moreover, continuous cutting avoids micro-indentations and other surface defects that can occur when the cutting process is stopped and restarted.
High Precision Applications
The serial line's precision and accuracy make it ideal for high-precision applications. Whether it's processing high-grade aluminum plates or mirror-finish stainless steel sheets, the serial line delivers unparalleled results. Short cutting lengths are no match for this robust system, ensuring that even the most delicate products are handled with care.
Advantages of Rotary Shear Technology
Enhanced Surface Quality
The continuous cutting process of rotary shear technology ensures a smooth and defect-free surface. This is especially crucial for applications where aesthetics and functionality are equally important, such as in the automotive and aerospace industries.
Increased Productivity
By eliminating downtime and minimizing waste, rotary shear technology significantly increases productivity. Manufacturers can now produce more products in a shorter time, meeting the demands of a fast-paced market.
Versatility
The serial line's ability to handle a wide range of materials and thicknesses makes it a versatile addition to any metal processing plant. From soft aluminum to hard stainless steel, this system can handle the job with ease.
Real-World Applications of Rotary Shear Technology
To illustrate the effectiveness of rotary shear technology, let's explore a few real-world case studies.
1. Aluminum Plate Processing
A leading aluminum manufacturer was struggling with surface defects caused by traditional shearing methods. After investing in rotary shear technology, the company experienced a significant improvement in surface quality, leading to increased customer satisfaction and sales.
2. Stainless Steel Sheet Cutting
A manufacturer of precision stainless steel components was unable to meet tight deadlines due to slow and inefficient cutting processes. By adopting rotary shear technology, the company was able to significantly increase production speed while maintaining high precision and accuracy.
Conclusion
Rotary shear technology has proven itself as an innovative solution in the metal processing industry. The serial line, with its ability to perform continuous cutting and handle a wide range of materials, offers unparalleled precision and efficiency. As the demand for high-quality metal products continues to grow, rotary shear technology will play an increasingly important role in meeting these demands.
www.wxbono.com
Bono Machinery
Average Rating