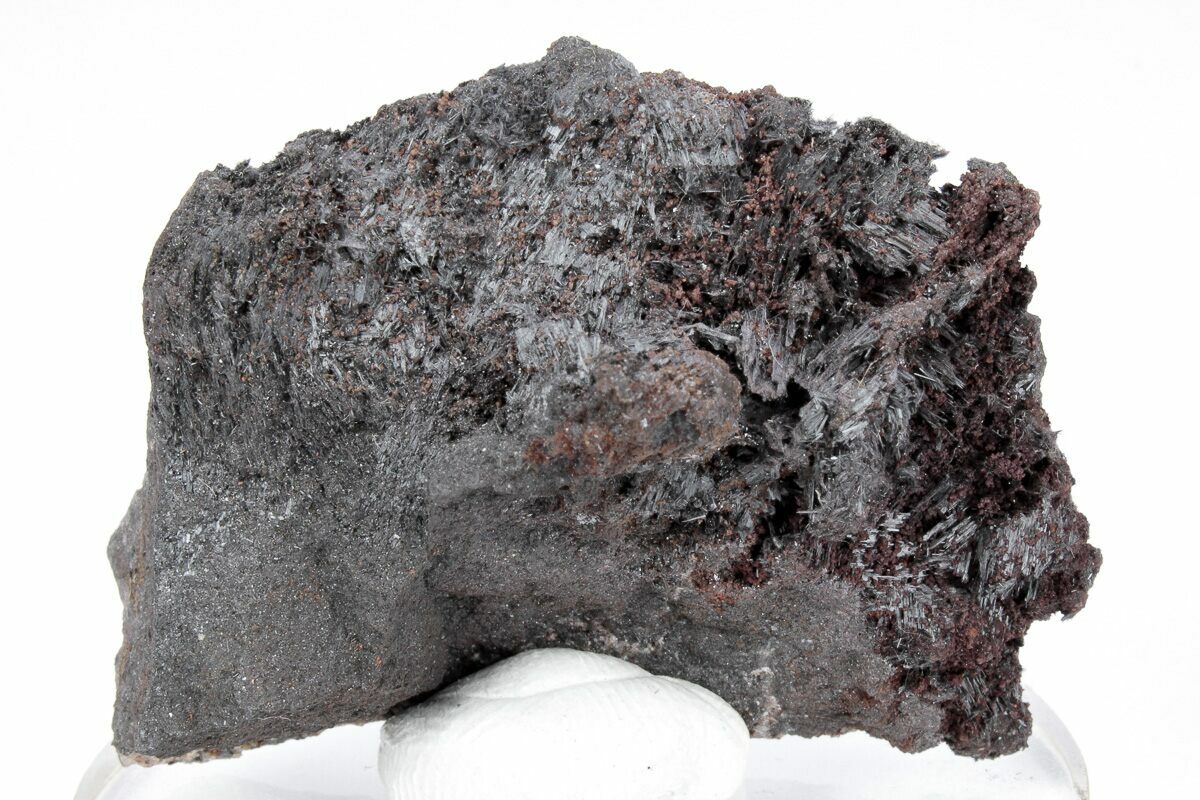
The Importance of Regular Calibration for Metal Detectors: Ensuring Optimal Performance and Safety
Metal detectors play a crucial role in various industries, including manufacturing, mining, food processing, and security. These devices are designed to detect metallic objects and ensure the safety and efficiency of operations. However, to maintain their accuracy and reliability, metal detectors require regular calibration. In this article, we will explore the significance of calibration, the recommended frequency for calibration, and the potential consequences of neglecting this essential maintenance task.
- Understanding Calibration:
Calibration is the process of adjusting and verifying the accuracy of a metal detector by comparing its readings to known standards. It involves fine-tuning the device to ensure it detects metal objects with precision. Calibration eliminates any deviations or inaccuracies that may occur over time due to environmental factors, wear and tear, or changes in the production process. - Factors Influencing Calibration Frequency:
The frequency at which metal detectors should be calibrated depends on several factors, including:
a) Usage Intensity: Metal detectors subjected to heavy usage, such as those in high-volume manufacturing facilities or busy security checkpoints, may require more frequent calibration. Frequent use can lead to faster wear and potential drift in accuracy.
b) Environmental Conditions: Harsh environments, such as extreme temperatures, humidity, or exposure to dust and contaminants, can affect a metal detector's performance. In such cases, more frequent calibration may be necessary to compensate for these adverse conditions.
c) Regulatory Requirements: Certain industries, such as food processing or pharmaceuticals, have strict regulations regarding metal detection. Compliance with these regulations often necessitates regular calibration and documentation to ensure product safety and quality.
- Recommended Calibration Frequency:
While the exact calibration frequency may vary depending on the factors mentioned above, a general guideline is to calibrate metal detectors at least once every six months. However, industries with higher risk factors or stringent regulations may require more frequent calibration, such as quarterly or even monthly. - Consequences of Neglecting Calibration:
Failing to calibrate metal detectors regularly can have severe consequences, including:
a) Reduced Detection Accuracy: Over time, a metal detector's sensitivity may decrease, leading to missed detections or false alarms. This can compromise the safety and quality of products, potentially resulting in costly recalls, customer dissatisfaction, or even legal liabilities.
b) Increased Maintenance Costs: Neglected calibration can lead to increased wear and tear on the device, resulting in more frequent breakdowns and repairs. Regular calibration helps identify and address minor issues before they escalate, reducing maintenance costs in the long run.
c) Non-compliance with Regulations: Industries with strict regulations, such as the food or pharmaceutical sectors, risk non-compliance if metal detectors are not calibrated as required. This can lead to penalties, loss of reputation, and potential business closures.
Conclusion:
Regular calibration is essential for maintaining the accuracy, reliability, and safety of metal detectors across various industries. By adhering to recommended calibration frequencies and considering factors such as usage intensity, environmental conditions, and regulatory requirements, businesses can ensure optimal performance, minimize risks, and uphold product quality. Neglecting calibration can have detrimental consequences, both financially and legally. Therefore, investing in regular calibration is a proactive measure that guarantees the continued effectiveness of metal detectors in safeguarding operations and enhancing overall productivity.
Average Rating