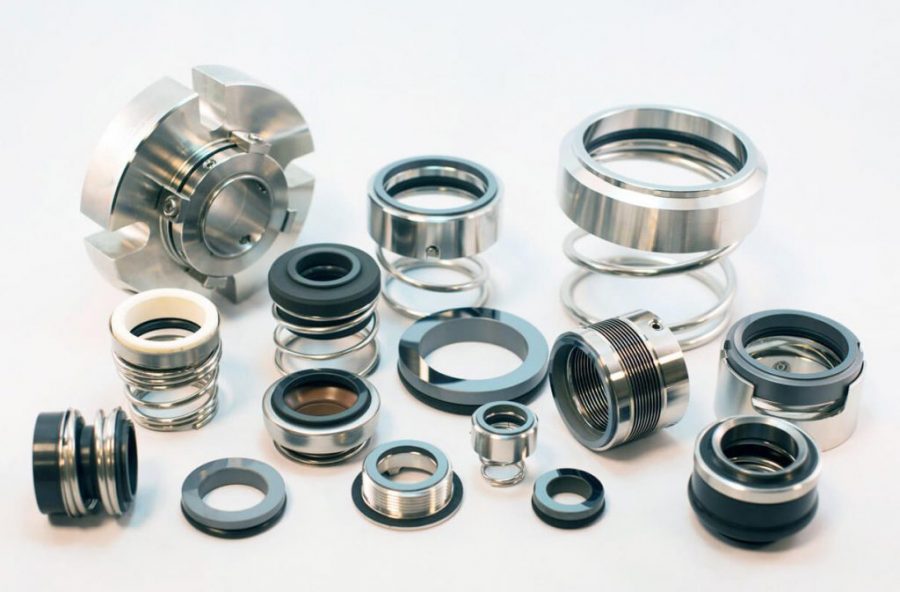
Balanced vs. Unbalanced Mechanical Seals: Understanding the Differences
Mechanical seals are critical components in pumps and other rotating equipment, used to prevent leakage of fluids and gases. There are two main types of mechanical seals: balanced and unbalanced. While both types serve the same purpose, they differ in their design and performance characteristics. In this article, we will explore the differences between balanced and unbalanced mechanical seals, and their respective advantages and disadvantages.
What is a Mechanical Seal?
Before we dive into the differences between balanced and unbalanced mechanical seals, let's first understand what a mechanical seal is. A mechanical seal is a device that creates a static seal between two surfaces, typically a rotating shaft and a stationary housing. It consists of two main components: a stationary component and a rotating component. The stationary component is typically mounted on the pump housing, while the rotating component is mounted on the pump shaft. When the pump is in operation, the rotating component rotates with the shaft, while the stationary component remains fixed in place. The two components are held together by a spring, which creates a seal between them.
What is a Balanced Mechanical Seal?
A balanced mechanical seal is designed to maintain a balance of forces across the seal faces, which helps to reduce wear and tear and increase the life of the seal. In a balanced mechanical seal, the seal faces are designed to be of equal size and shape, and the spring that holds the two components together is located in the center of the seal. This design helps to distribute the load evenly across the seal faces, which reduces the risk of distortion and wear.
Advantages of Balanced Mechanical Seals:
- Reduced wear and tear
- Longer seal life
- Reduced risk of leakage
- Suitable for high-pressure applications
What is an Unbalanced Mechanical Seal?
An unbalanced mechanical seal, on the other hand, is designed to create a seal by applying a greater force on one side of the seal faces than the other. This design is typically used in low-pressure applications, where the forces acting on the seal faces are relatively low. In an unbalanced mechanical seal, the seal faces are of different sizes and shapes, and the spring that holds the two components together is located off-center.
Advantages of Unbalanced Mechanical Seals:
- Lower cost
- Suitable for low-pressure applications
- Simpler design
Disadvantages of Unbalanced Mechanical Seals:
- Higher risk of wear and tear
- Shorter seal life
- Higher risk of leakage
- Not suitable for high-pressure applications
Conclusion:
In summary, the choice between a balanced and unbalanced mechanical seal depends on the specific application and operating conditions. Balanced mechanical seals are generally preferred for high-pressure applications, where the forces acting on the seal faces are high, and a longer seal life is desired. Unbalanced mechanical seals, on the other hand, are suitable for low-pressure applications, where cost and simplicity are more important than seal life. By understanding the differences between these two types of mechanical seals, you can make an informed decision when selecting the right seal for your application.
Average Rating