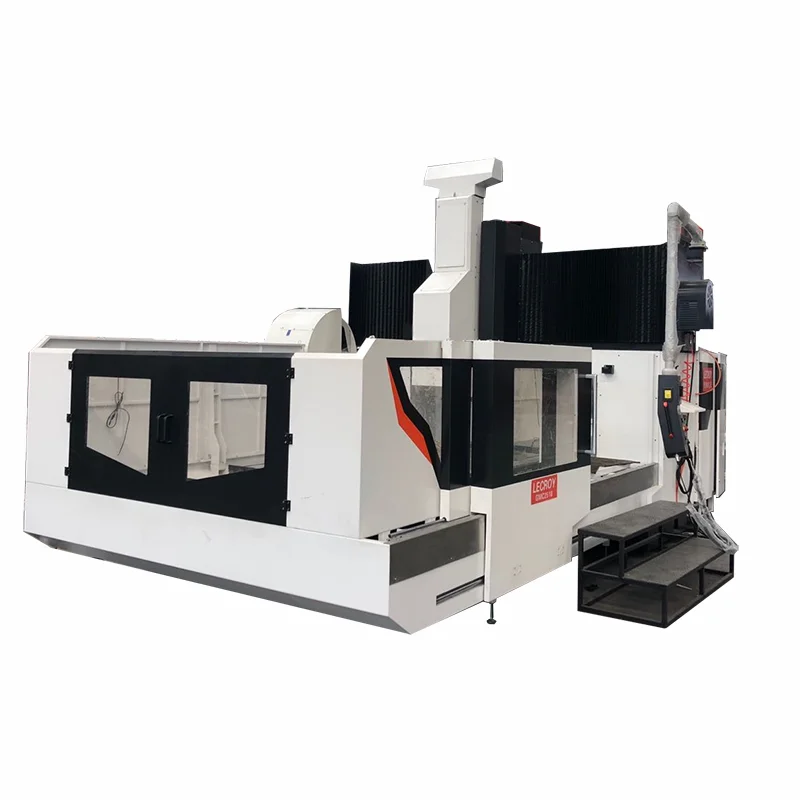
How to improve the processing efficiency of gantry CNC milling machine?
As a high-precision and high-efficiency CNC processing equipment, gantry CNC milling machine plays a vital role in modern manufacturing. It is widely used in machinery, aerospace, automobile manufacturing, mold processing and other fields, especially in the processing of heavy and large-size workpieces, showing irreplaceable advantages. With the continuous improvement of market requirements for product quality and production efficiency, improving the processing efficiency of gantry CNC milling machine has become the goal pursued by manufacturing companies. This article will explore how to improve the processing efficiency of gantry CNC milling machine from multiple angles, including equipment optimization, processing technology improvement, operation skills improvement, automation technology application and other aspects.
To improve the processing efficiency of gantry CNC milling machine, we must first clarify several core dimensions of efficiency: processing speed, processing accuracy and equipment utilization. Processing speed and accuracy are the most direct influencing factors, and the efficient use of equipment is related to the shortening of the overall production cycle. Therefore, the key to improving the processing efficiency of gantry CNC milling machine is to optimize the processing process, improve equipment performance, reduce non-productive time, and ensure stable processing accuracy.
1. Optimize processing technology
1.1 Reasonable selection of tools and cutting parameters
The selection of tools directly affects processing efficiency and processing quality. For gantry CNC milling machines, the material, shape, coating and cutting angle of the tool need to be selected according to factors such as the processing material, processing accuracy requirements and tool life. Suitable tools can not only improve processing efficiency, but also effectively extend the service life of the equipment.
In addition, the optimization of cutting parameters is also a key factor in improving processing efficiency. The feed speed, cutting depth, cutting width and other parameters of the tool need to be reasonably set according to the material and geometry of the specific workpiece. Appropriately increasing the cutting speed and feed rate can significantly improve the processing efficiency, while reducing the processing time while ensuring the processing accuracy.
1.2 Multi-process parallel and compound processing
When processing complex workpieces, the traditional single-process processing method often cannot give full play to the advantages of CNC milling machines. Therefore, the use of multi-process parallel processing is an effective means to improve processing efficiency. Gantry CNC milling machines usually have multiple axial motion functions, and can reduce the number of tool changes and process conversion time by reasonably planning the processing route.
The introduction of compound processing technology, such as completing multiple processes such as milling, drilling, and tapping at the same station, can also greatly improve efficiency. Through compound processing, the time for fixture replacement and clamping adjustment can be reduced, thereby improving overall production efficiency.
1.3 Optimize the use of cutting fluid
Cutting fluid plays a role in cooling, lubrication and cleaning in CNC milling. Reasonable use of cutting fluid can not only increase the service life of the tool, but also improve cutting performance and improve processing efficiency. In high-load processing, the selection and spraying method of cutting fluid are particularly important. Appropriately increasing the flow rate of cutting fluid and improving the cooling effect can effectively reduce cutting heat and prevent overheating, thereby improving processing accuracy and processing speed.
2. Improve equipment performance
2.1 Improve machine tool rigidity
Machine tool rigidity is a key factor affecting processing accuracy and efficiency. The rigidity of the gantry CNC milling machine is mainly reflected in the stability of the machine tool structure and moving parts. In order to improve processing efficiency, it is first necessary to ensure that the rigidity of the machine tool structure is strong enough to avoid processing errors caused by vibration during processing.
In addition, the rigidity and stability of the machine tool's guide rail system, spindle and other components are also crucial. Strengthening the design and material selection of these key components can effectively improve the rigidity of the gantry CNC milling machine, reduce vibration, and thus improve processing accuracy and efficiency.
2.2 Regular maintenance and care
Regular equipment maintenance and care are important guarantees for the long-term and efficient operation of the gantry CNC milling machine. Regularly checking the lubrication system, drive system, sensors and other components of the machine tool can timely discover potential fault hazards and avoid downtime and reduced production efficiency caused by equipment failure.
In addition, cleaning, precision correction, and wear detection of components are also key to ensuring stable operation of the equipment. Through reasonable maintenance and care, the service life of the equipment can be extended, processing efficiency can be improved, and downtime can be reduced.
2.3 Upgrading control systems and software
Modern CNC milling machines are increasingly dependent on intelligent control systems. Upgrading CNC systems and software can achieve more precise processing control and more efficient programming functions. For example, the optimized control system can automatically adjust the cutting parameters to adapt to different processing requirements by real-time monitoring of the processing process, thereby improving processing efficiency.
In addition, cutting optimization software and dynamic compensation technology based on advanced algorithms can also effectively improve the processing efficiency of gantry CNC milling machines. These intelligent technologies automatically optimize cutting parameters and reduce unnecessary motion paths by analyzing various factors in the processing process, thereby maximizing the processing efficiency of the equipment.
3. Operating skills and employee training
3.1 Strengthening employee operating skills training
The skill level of the operator has a direct impact on the processing efficiency. By providing professional training to the operator and improving his proficiency in the operation of the gantry CNC milling machine, the downtime and processing errors caused by improper operation can be effectively reduced. The training content should include equipment operation specifications, processing skills, program writing, troubleshooting, etc., to ensure that the operator can deal with problems in a timely manner when encountering problems and maintain the efficient operation of the equipment.
3.2 Strengthen the adjustment of process parameters
Different workpieces have different processing requirements. Operators need to flexibly adjust the processing parameters according to the specific conditions of the workpieces. Proficiently mastering the processing characteristics of workpieces of different materials and shapes can effectively avoid inefficiency and processing quality problems caused by improper process parameters.
Improving the processing efficiency of the gantry CNC milling machine not only depends on the performance of the equipment itself, but also involves many factors such as process optimization, automation technology, and operator skills. By rationally selecting cutting tools and cutting parameters, optimizing machining processes, improving equipment performance, introducing automation technology, and strengthening operator training, we can effectively improve machining efficiency, shorten production cycles, reduce production costs, and help manufacturing companies gain advantages in the fiercely competitive market.
As a gantry CNC milling machine manufacturer, we are always committed to providing customers with high-performance and efficient machining solutions. We also provide regular maintenance and training services to help customers maximize the service life and machining capabilities of their equipment.
www.bofengmachinery.com
bofengmachinery
Average Rating