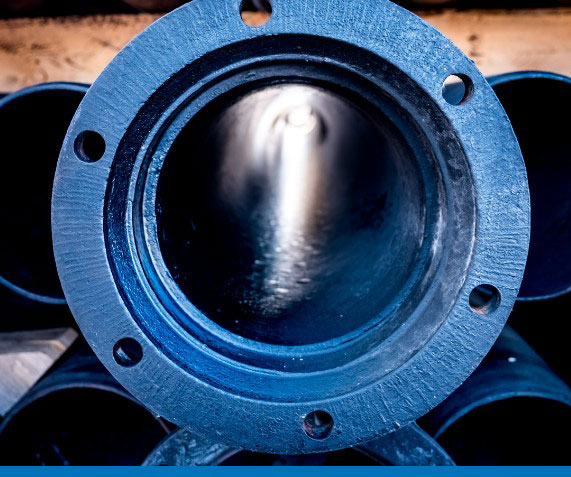
The Keystone of Engineering Precision: Unraveling the Significance of Welding Joints
In the intricate world of engineering, welding joints stand as the linchpin, holding together structures that define our modern infrastructure. This article delves deep into the profound importance of welding joints, exploring the multifaceted reasons that make them indispensable in various industries.
1. Structural Integrity and Strength
A. Fusion of Materials
At its core, welding involves the fusion of materials, creating a bond that surpasses the strength of the individual components. Explore how this fusion contributes to the structural integrity of welded joints, enabling them to withstand diverse mechanical stresses and loads.
B. Uniform Distribution of Forces
Examine how welding allows for the uniform distribution of forces across the joint, preventing concentration points of stress that could lead to premature failure. This aspect is crucial in applications ranging from construction to automotive manufacturing.
2. Seamless Integration in Fabrication
A. Continuous Material Flow
Discuss the seamless integration achieved through welding, where molten materials flow and solidify, eliminating gaps or weak points. This ensures a homogenous structure, particularly vital in critical applications like aerospace engineering.
B. Precision in Fabrication
Explore how welding provides precision in fabricating complex structures. The ability to join materials with intricate shapes and designs contributes to the creation of components that meet exact specifications, enhancing overall product quality.
3. Versatility in Material Compatibility
A. Joining Diverse Materials
Highlight the versatility of welding in joining diverse materials, from metals to plastics. Discuss specific welding techniques that accommodate different material properties, enabling engineers to design hybrid structures that optimize performance.
B. Overcoming Material Limitations
Examine cases where welding plays a pivotal role in overcoming material limitations. For instance, welding dissimilar materials allows for the creation of components with enhanced characteristics, such as improved corrosion resistance or conductivity.
4. Economical and Efficient Production
A. Single-Step Fabrication
Discuss how welding facilitates single-step fabrication, streamlining production processes. This efficiency not only reduces manufacturing costs but also accelerates project timelines, making welding a cornerstone in industries with high-volume production requirements.
B. Resource Optimization
Explore how welding contributes to resource optimization by minimizing material waste. The precision in joint formation ensures that materials are utilized effectively, aligning with sustainability goals in modern manufacturing.
5. Repair and Maintenance
A. Restoration of Structural Integrity
Examine the role of welding in repair and maintenance, where it serves to restore the structural integrity of components. Whether in automotive repair or the maintenance of industrial machinery, welding plays a vital role in extending the lifespan of structures.
B. Cost-Effective Repairs
Discuss how welding allows for cost-effective repairs compared to complete component replacement. This aspect is particularly significant in industries where downtime is critical and cost-efficiency is paramount.
Conclusion: Welding Joints as the Backbone of Innovation
Summarize the article by emphasizing how welding joints serve as the backbone of innovation in engineering and manufacturing. The ability to create strong, precise, and versatile joints propels advancements across various industries, shaping the world we live in.
Average Rating