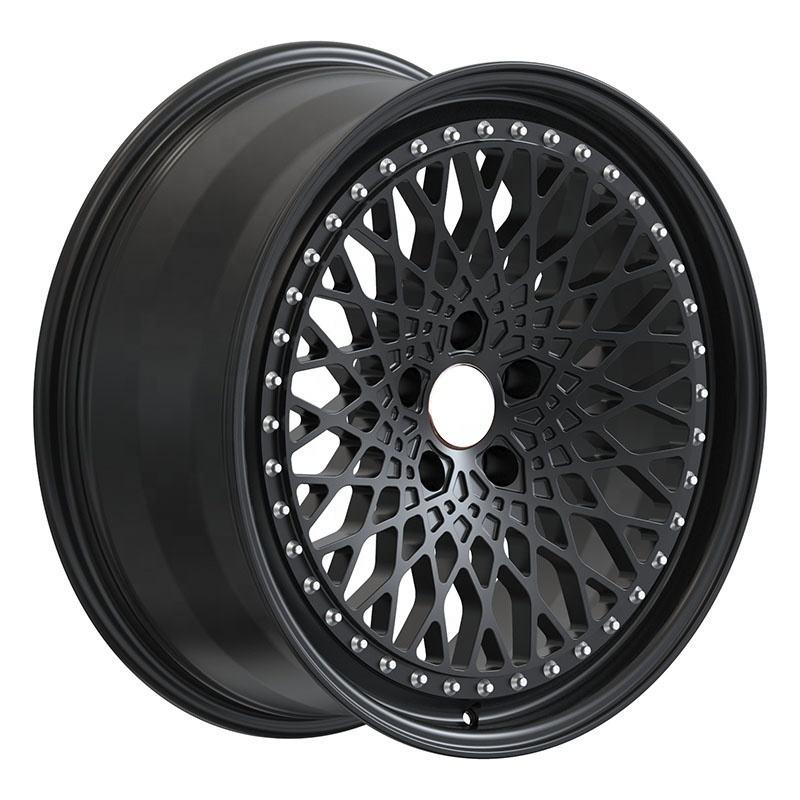
Manufacturing Process of 18 Inch Car Forged Aluminum Alloy Wheel Hub
The automotive industry is continuously evolving, with a focus on enhancing performance, efficiency, and aesthetics. One of the critical components that contribute to these aspects is the wheel hub. Ouya will share with you the manufacturing process of the high-performance 18 inch car forged aluminum alloy wheel hub, from design to final product.
Design and Material Selection
1. Design Considerations: The design phase is where the concept of the wheel hub is born. Engineers consider factors such as load-bearing capacity, aerodynamics, and compatibility with various car models.
2. Material Selection: Forged aluminum alloy is chosen for its strength-to-weight ratio, corrosion resistance, and heat dissipation properties. The alloy typically consists of aluminum with trace amounts of copper, magnesium, and silicon.
Forging Process
1. Heating: The aluminum alloy is heated to a specific temperature, usually between 400°C to 500°C, to make it malleable for forging.
2. Forging: The heated alloy is then placed in a die, which is a mold with the desired shape of the wheel hub. A hydraulic press or hammer applies immense pressure, causing the metal to flow and take the shape of the die.
3. Precision Forging: This step ensures that the wheel hub meets exacting specifications. It involves using a forging press with computer numerical control (CNC) to achieve high levels of precision.
Cooling and Heat Treatment
1. Cooling: After forging, the wheel hub is cooled slowly to room temperature to relieve internal stresses and to prevent cracking.
2. Solution Heat Treatment: This involves heating the wheel hub to a specific temperature (around 500°C) and holding it there for a period, followed by rapid cooling. It helps to soften the metal and make it more amenable to further processing.
3. Aging: The wheel hub is then subjected to a controlled heating and cooling process to strengthen the alloy and enhance its mechanical properties.
Machining and Finishing
1. Machining: The wheel hub undergoes various machining processes such as turning, milling, and drilling to achieve the final dimensions and features like bolt holes and spoke patterns.
2. Inspection: Each wheel hub is inspected using precision measuring tools and optical scanners to ensure it meets the design specifications.
3. Finishing: The wheel hub is polished to remove any machining marks and to achieve a smooth, aesthetically pleasing surface. It may also undergo anodizing or powder coating for enhanced durability and appearance.
Quality Control and Testing
1. Visual Inspection: A thorough visual inspection is conducted to check for any surface defects or irregularities.
2. Dimensional Testing: The wheel hub's dimensions are checked against the design specifications using advanced measuring equipment.
3. Dynamic Testing: The wheel hub is mounted on a specialized machine that simulates various driving conditions to test its structural integrity and performance.
4. Load Testing: It is subjected to a load test to ensure it can handle the weight and forces exerted during regular use.
Assembly and Packaging
1. Assembly: The wheel hub is assembled with other wheel components such as the tire, brake rotor, and bearings.
2. Final Inspection: A final inspection is conducted to ensure that the assembled wheel meets all quality standards.
3. Packaging: The wheel is carefully packaged to protect it during transportation and storage.
Conclusion
The manufacturing process of an 18-inch car forged aluminum alloy wheel hub is a complex and meticulous journey from design to the final product. It involves a blend of advanced technology, skilled craftsmanship, and rigorous quality control. The result is a wheel hub that not only enhances the performance and aesthetics of a vehicle but also provides durability and reliability for a safe and enjoyable driving experience.
https://www.ouyawheel.com/Manufacturing-Process-of-18-Inch-Car-Forged-Aluminum-Alloy-Wheel-Hub.html
Ouya
info@ouyawchina.com
Average Rating